When it comes to ERP, many manufacturers have chosen the “path of least resistance,” continuing to use the same legacy systems they’ve had for the past 15 to 30 years. Familiarity with on-premise architecture has lulled these companies into a false sense of comfort with the status quo, but in reality, they’re stuck in a business era long gone. As time passes, these companies risk missing opportunities to achieve increased growth, customer centricity, recruitment of new knowledge workers, and other competitive advantages – all of which could result in greater costs and risks in the end.
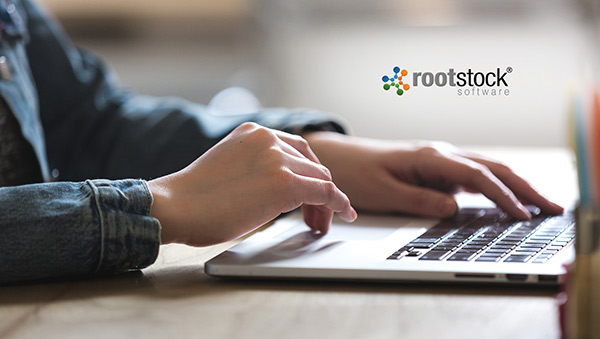
The reasons for wanting to hold onto an existing legacy system are well known and understandable. Corporate leaders feel replacement will be expensive and resource intensive, not to mention accompanied with a significant risk of project failure. Many believe the current system, which was built and honed over time to produce a competitive advantage, still works and retiring it could jeopardize key operations. If the system has been highly customized, it may seem daunting to reconfigure a new solution from scratch. And of course, no one likes change. With a large system replacement, there’s significant internal resistance to overcome, not to mention the legwork to obtain buy-in for the project. With all of these factors, it’s no wonder companies try to put off the inevitable.
But as time goes on, companies must also consider the large-scale benefits they’re losing out on by not making the switch to a cloud ERP sooner:
Opportunities for growth
Let’s face it: companies want to be on the leading-edge. They want to achieve first-to-market or other competitive advantages. However, a slow-moving legacy ERP holds them back. Continued growth is predicated on the ability to adapt, respond, scale, and automate. So, the lack of agility in legacy systems leads to an inability to stay competitive, which can translate into reduced revenue and losing one’s edge over time.
Although a legacy system may be able to perform its original core functions with ongoing maintenance, those functions may no longer serve a company’s business or customer needs. For example, a legacy ERP might not be able to support increased production, which often requires a more sophisticated supply chain or rapid launch of new products.
Companies also have evolving technology needs. Currently, many manufacturers are looking to incorporate the Internet of Things (IoT) or 3D printing into their operations. Legacy ERP systems can only keep pace with new technology for so long. Beyond that, a company may be forced to adapt its business to system’s limitations, stunting its ability to grow or leverage emerging options.
Reducing IT maintenance costs
It comes as no surprise that the older and more complex a legacy system, the more it costs to operate and maintain. First of all, legacy systems require a stack of software, security and hardware that has to be constantly managed and updated. Companies can eliminate these costs when they adopt a cloud ERP solution. Cloud systems also reduce the need for costly maintenance. These funds can then be redirected toward new initiatives and innovation. Computer Economics estimates that companies using legacy systems spend about 80% of their IT budgets on maintaining existing systems, with only 20% left for new initiatives. Computer Economics also projects that after moving to the cloud, companies utilize only 69% of IT budgets for support, with as much as 31% directed toward new initiatives – a significant improvement.
Implementing a customer-centric focus
Customer-centric manufacturing isn’t just the latest buzzword. It’s a real shift in strategy that puts the customer first, both in terms of products and service. Companies are striving to satisfy heightened customer expectations, provide more personalized products and offer top-notch service.
Legacy ERP systems don’t effectively support the infrastructure for customer-centric manufacturing. At the core of customer-centric manufacturing is the need to aggregate, share, and act on data. However, with a legacy ERP, data is typically fragmented and disconnected between departments and business functions. One department may have customer data while operational departments have another set, and the systems don’t talk to one another. Customer service representatives may not have access to all the information they need to address customer concerns. Over time, multiple sets of competing information can result in lost revenue as customers seek more responsive service elsewhere.
A 360-degree view of customers and operations
Another primary example of the disconnection introduced in the section above is the fact that legacy ERP systems aren’t typically connected to CRM systems. Key processes and data are kept in silos, making it difficult for companies to effectively know and respond to their customers. In addition, there’s an inability to see company-wide trends and results as data and transactions are caught in the CRM / ERP divide. In essence, a legacy ERP hinders executives from obtaining a complete view of their business, while a true cloud ERP would provide the 360° view that enables companies to synchronize operations with market demand. Companies also gain complete visibility of customers, so they can meet their needs from order to delivery.
Adapting to other market and industry needs
As manufacturers try to adapt their production environment to the demands of modern manufacturing, they quickly realize the significant gap that exists between what they need and what their legacy ERP can deliver. While cloud ERP can help companies modernize and achieve digital processes, legacy systems create bottlenecks that work against these efforts to bring manufacturing into the 21st century.
To support today’s modern manufacturing needs, companies need speed and flexibility in their ERP – features not found in a legacy system. In addition, many employees – baby boomers and millennials alike – prefer to utilize smartphones, rather than laptops and tablets. However, legacy systems aren’t designed to accommodate a mobile workforce. Their functions and data are centralized and disconnected, making it difficult for people to communicate, access information, and make decisions. Cloud ERP, on the other hand, has mobility built-in, so users can readily access ERP capabilities via their smartphones.
According to Gartner, companies that continuously improve their operations via a cloud ERP will realize 60% more business value simply by adopting the latest best practices the vendor offers via their frequent SaaS releases.
Connecting people, data, and things
Manufacturers have significant data to manage, including data regarding marketing and sales, customers, suppliers, products, financials, engineering and inventory, production, shipping and receiving, and service. All of this information needs to be digitally shared with the right people at the right time – both inside the company and externally with suppliers, partners, and customers. According to a 2018 study by Aberdeen Group, top performing companies are 46% more likely than other companies to be able to share data with both customers and suppliers.
Rather than facilitating this function, legacy systems inhibit it, as they are notoriously difficult to integrate. A cloud ERP platform, with its inherent connectivity, can securely share ERP data for the benefit of customer and supplier communities, as well as using data from remote IoT apps.
Attracting new knowledge workers
One of the biggest challenges facing manufactures is the labor shortage. In a recent survey, the National Association of Manufacturers (NAM) projected a shortfall of almost eight million workers by 2030, and bringing with it, potential revenue losses as high as $600 billion.
As baby boomers retire in rapidly increasing numbers, manufacturers need to be able to attract young, digitally-proficient workers. Digital transformation is one way to make the manufacturing industry more attractive to these new knowledge workers. For example, a twenty-something won’t want to spend all day on a legacy ERP system that’s 15 to 30 years old. They’ve grown up living and working on smart phones and social media, and they expect ERP systems to operate similarly. If these technologies are not available in the manufacturing industry, young workers will seek jobs elsewhere.
The longer you wait, the greater the risk
Legacy systems are becoming increasingly more difficult to maintain, especially as the hardware and software supporting them turn obsolete. Likewise, IT professionals who have maintained legacy systems are retiring or moving to the more in-demand and higher-paying positions associated with the cloud. As businesses continue to hold onto legacy systems, the greater the risk that these systems will finally fail. Waiting too long to upgrade can also make data conversion and process engineering more prone to risk. As discussed, the IT professionals – who originally built these legacy ERP systems and know how these systems handled data and business processes – are leaving. As they go, a company’s institutional knowledge goes with them. Once it’s lost, it cannot easily be baked into a new system rollout. If day-to-day business processes weren’t properly documented, it could increase the risk of project failure.
As we’ve outlined, it’s crucial that companies with outdated ERPs consider a switch to a more modern, cloud solution sooner rather than later.