This is the second in a series of brief articles describing what business activities should be undertaken before an ERP implementation, and it focuses on one of the most important data objects: materials.
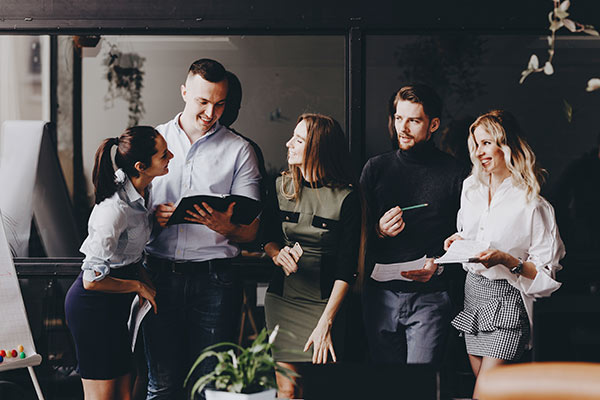
A very common mistake that many organizations make when they first migrate to an ERP system is failing to put in the up-front time and effort to streamline the materials, and material-plant combinations in their current system. In fact, some organizations fail to do any in-depth analysis at all and take the extreme position to “migrate all materials and extend them everywhere for now” expecting to be able to sort it out after go-live (something much easier said than done). Although I am convinced this approach is born mostly out of naivety (and let’s be honest – perhaps also a bit out of laziness) many organizations will try to justify this approach by claiming it “helps them ensure they maintain the most flexible supply chains possible”. To that response I say “rubbish!” Over the years I have seen many organizations make this choice, but I have never seen any – not even one – who were happy after go-live that they did.
As troubling and pervasive as this phenomenon is, I can sort of understand how that can happen to an organization migrating to an ERP system for the first time. After all, you don’t know what you don’t know. But what troubles me even more is that I see so many organizations who made that mistake years ago, fail to correct it in subsequent implementations and upgrades. Why? It’s simply easier to migrate what you already have set up, than to rework it and do it right. Easier, yes, but this mistake results in a new system built upon a “pass the trash” data foundation.
So, whether you are migrating to an ERP system for the first time, or the nth time, here are 5 reasons why you should put significant pre-project effort into streamlining your material and material-plant combinations.
Data quality will improve
This one is a no-brainer. As an organization puts a given amount of effort into their data preparation, it stands to reason that if that effort is focused on a smaller data footprint, the relative effort per material-plant combination will increase and the overall data quality will improve.
Ongoing data maintenance will decrease
This one too, is a no-brainer. If you have a smaller data footprint, the ongoing data maintenance will continue to be smaller going forward. Consider, for example, how every manufactured material requires a BOM for every plant where it is manufactured. Of course, if a material truly is routinely manufactured at multiple plants, then by all means, set up and maintain the material-plant combinations and all required BOMs. If, however, you are contemplating setting up a material-plant combination because “one day we just might want to manufacture this part at another plant”, I caution against that. I have seen far too many “maybe” scenarios never happen, and the data maintenance team is saddled with both creation and ongoing maintenance of never-used data elements for the life of the ERP system. This is a tremendous waste of valuable data maintenance resources. They should be laser focused on the critically important data rather than diluting their efforts with the “might never happen” scenarios.
“Skeletons in the closet” will be exposed
To properly streamline materials and material-plant combinations it is necessary to thoroughly investigate and characterize where and how materials are used. The fact that a given material has inventory means something must be done with it either before or during migration. If the inventory is healthy and active, then setting up the materials and migrating the inventory to the new system makes sense. If the inventory is inactive and/or obsolete, however, then the organization must decide what to do with it. Can the product be reworked and sold, or must it be disposed of? Equally important is understanding how it came to be. Was this the result of an over-make by Manufacturing? A poor forecast by Sales? A cancelled sales order? A quality issue? Has the underlying cause been resolved, or is it continuing? Is this symptomatic of a larger underlying issue? Understanding and addressing these sorts of questions will provide great insights into both the organization’s capabilities and mindsets. This is often a rich source of improvement opportunities and organizations are wise to address these deficiencies early and often.
Product portfolio improvements naturally follow
In characterizing materials, it is helpful to define the specific attributes used to identify individual products. In doing so, it is common to find that two or more materials have the same, or nearly the same, attributes. This implies that there are either redundant materials, or that some important and distinguishing attributes are missing. Regardless of which situation it is, just the mere process of chasing down that answer often brings about an enlightened understanding of the product portfolio and leads to questions such as “why do we have so many materials that appear to be so close in fit, form and function?” Addressing that question satisfactorily can take months, so clearly this is something best done well before the formal ERP project kicks off.
It will reduce operational mistakes
Most ERP systems have advanced search functionality that enable users to rapidly find materials, plants, storage locations, and the like. Unfortunately, most ERP systems don’t have a foolproof mechanism to help users discern between material-plant combinations genuinely intended for use and those set up “just in case someday we might want to use it”. Therefore, having both flavors of choices available to users is just begging for mistakes to be made. The best way to avoid these types of mistakes is simply to not even set up non-intended options in the first place.
In summary, when it comes to materials and material-plant combinations, less truly is more. In my experience, it is much better to have a minimal data footprint of excellent quality, than a broad data footprint of lesser quality. Yes, occasionally the data team will have to expedite the set-up of a new material here and there, but that is a small price to pay for achieving extremely high data integrity. As I’ve mentioned in previous posts, every migration to a new system is an opportunity for an organization to put past sins behind them, wipe the slate clean, and make a fresh start. Take advantage of that opportunity by starting early!
Please share any thoughts, comments, or relevant experiences you may have, and stay tuned for the next in this series of articles.