Anyone who has ever spent even a little time in an ERP system understands all too well the meaning of “garbage in, garbage out”. ERP systems are incredibly powerful and complex and, generally speaking, very good at what they do, however, they all share one common Achilles heel: they actually believe the underlying data – both master data and transactional data – that controls them. When that data is an accurate representation of the physical world, life is good! When it is not, life in an ERP environment can be unbearable! That is why it is so important to take proactive steps to get the data right.
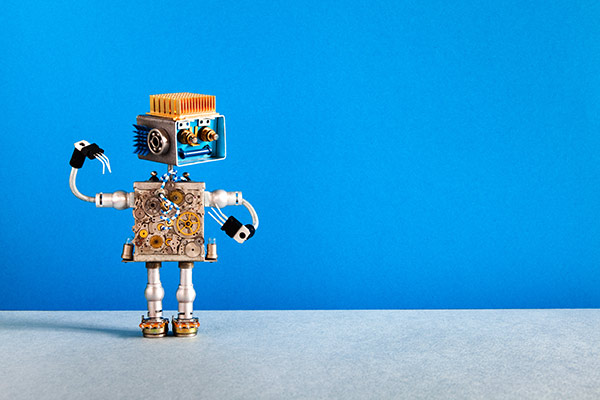
Part of the challenge with ERP systems is that they still rely heavily on human inputs, and let’s face it, humans make mistakes. Although I think most organizations would find it to be a rather large leap to take humans completely out of the data equation, I do believe IoT has much to offer in helping make sure humans “get it right” when it comes to transactional and master data in ERP systems. What follows is a simple example of how IoT, and other Industry 4.0 concepts, can be applied to continuous, semi-continuous, and even batch manufacturing processes, to greatly improve ERP data integrity.
To see the value of this IoT use case, I will jump to the last chapter of the book, so to speak, to describe the end state, and then go back and fill in what specific steps it takes to get there.
First, let’s look at what happens with material movement validation. In the traditional approach, the shift supervisor may do a quick check at the end of every shift to confirm that the reported total production on his/her shift makes sense for the machine rate and uptime for that day. This check is often an informal, back-of-the-envelope calculation without machine assist. Gross errors are generally identified and investigated in this approach, but more subtle errors often go undetected.
Adding just a little bit of extra measurement and analytical capability, can change the picture dramatically. With those things in place, two sets of checks can be performed automatically, multiple times during a shift, using real-time analytics and algorithms. The first check is a comparison of actual goods issues and receipts versus planned goods issues and receipts. This check helps assess how well the team is performing relative to plan, both in terms of total output and the relative ratio of ingredients. The second check is a comparison of all mass balance relationships to determine if anything has gone awry, such as, for example, a missing or errant goods movement, or a drift in measurement equipment calibration. While actual production may differ from planned production for any number of legitimate reasons, the mass balance checks should always hold true because the law of conservation of mass is universally true. Therefore, any discovered mass balance discrepancies trigger immediate corrective action response from the shift team. This not only greatly improves transactional data integrity; it also improves shift team participation and ownership.
But it’s not just about transactional data. The impact of added IoT capability can be extended to master data processes as well. In the traditional master data maintenance approach, BOMs and routes are reviewed annually as part of the process for setting standard costs. Typically, an overall variance analysis might be performed on each finished good, based on the cumulative variances for all the manufacturing orders over the past year. Depending upon the number of materials and production campaigns, this can be a rather time-consuming process. It also happens to be very much a “looking in the rear-view mirror” approach.
Contrast that to performing real-time trend analyses enabled by Big Data. Based on the real-time monitoring of material movements described above, it is now possible to automatically create and manage on-going control charts on every material, component, and asset. In essence, you can now constantly monitor BOM and route performance, raise real-time alerts, and take corrective action whenever appropriate. What once was an annual data analysis nightmare, is now performed in the background, constantly throughout the year, and available at your fingertips with the click of a button. No longer do you have to wait for “standard-setting season” to act.
Of course, there is some price to pay for all this capability, but it’s not as expensive as you might think. In addition to developing an application to execute and display the digital activities previously described, the following items must be put in place:
- Measurement capability – You must be able to measure and electronically report mass flow on every material stream – including waste and by-products. For most organizations, that capability exists for the intended produced material, and all ingredient streams, but it is the waste and by-product streams that typically require additional investment.
- Real–time material movements – Even if your organization is not quite ready for material movements to be autonomously generated directly from machines, you will need to have in place real-time (or near real-time) posting of material movements.
- Master Data Set-up – BOMs must contain all materials, including waste and by-product materials, in ratios based on actual demonstrated performance. The routes must contain rates which are likewise based on actual demonstrated performance.
- Algorithms – Logic must be developed to enable comparison of the actual measured values to the expected values as indicated in the BOMs and routes. That logic is based largely on the mass balance relationships of the components.
So, while implementing this IoT use case certainly isn’t free, it also is not exorbitant, and I believe most organizations will find the benefits to be well worth the price of admission.
This is just one simple example of how IoT and other Industry 4.0 concepts can be applied to improve data integrity in an ERP system. The number of other possible IoT use cases in ERP are as limitless as your own imagination. As you think through your overall IoT strategy, I encourage you to dream big but, implement in little bite size pieces. As we have just seen, even a light-touch IoT application, if well thought out, can greatly improve your overall ERP operational experience, and enhance your return on investment.