There’s no lack of published information on the enormous potential capabilities span, interoperability, and ultimate benefits of enterprise resource planning (ERP), product lifecycle management (PLM), customer relationship management (CRM), supplier relationship management (SRM), and other enterprise solutions in the manufacturing sector. Similarly, there’s also a plethora of research on these enterprise solutions’ pain points, implementation delays, and buyers’ remorse.
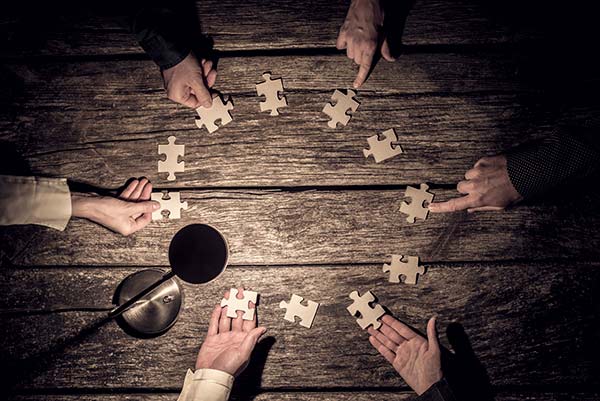
But difficult or easy, companies need ERP systems and related enterprise software solutions to streamline business processes, connect suppliers and partners, and manage the complexity that accompanies growth. So it’s no surprise that there is still a sizeable and growing buyer pool for ERP software solutions even 40+ years after their initial introduction: the ERP software market is expected to reach $ 41.69 Billion, globally, by 2020. With such big dollars on the table, it’s understandable that there are still literally hundreds of vendors providing solutions in this space, all wanting even a small piece of this giant revenue pie.
If manufacturers’ ERP and PLM software solutions are so comprehensive and there are so many vendors servicing this space, why are there still solution holes (the so-called “software fatal flaws”)? What are these shortcomings and what negative impact do they have on companies?
The Technology Tower of Babel
Like
the mythical Tower of Babel, ERP software has followed a similar pattern
of confluence, but instead of multiple peoples/civilizations converging in one
place, we have multiple technologies, data sources, and business participants
all trying to do the same thing as the people of Babel: communicate and
act. In theory, and in a world of published application programming
interfaces (APIs), web services, open source claims, etc., information in any
format should flow
accurately, automatically, and imperceptibly to any defined set or subset of
users for specific purposes. In practice, however, what often occurs is
altogether different: there is cacophony, not cohesion, in business data and
processes.
The reasons for this discord are plentiful, including:
- Siloed business data exists in both manual and digital form, both structured and non-structured (multi-media) data;
- Purpose-built enterprise applications are installed that are very good at solving one problem, but not another;
- New and different user/partner/customer pools continuously change and evolve;
- New products, new industry trends, legal and compliance developments, internal shifts, or other mandates (like product labeling) require either new reporting, analytics, or processes.
What we need from our business
data (and the processes related to that data) is easy-to-access, automated,
singular, and aggregated (single) versions of data “truth.” Such integrated,
reliable, and available data is needed for various critical manufacturing and
general business operations activities.
What is currently happening in process manufacturing companies (and which gets
exponentially worse based on the business’ complexity and/or size) is that
ERP/PLM and other appended solutions alone don’t adequately address a host of needs.
All too often, the band-aid fix is that companies are currently managing
various needs across a wide spectrum of product specs requirements, supplier
management, facility certifications, customer orders, and legal/compliance
mandates—via a variety of manual and/or redundant processes.
Where Advanced Process and Document Management Solutions Also Fall Short
What’s important to manufacturing companies is not only having access to their business and operational data (as important as that is), it’s also the method of getting access (i.e., “how” they get it) and the ultimate, often cross-purpose, usage of it (i.e., “what” they will do with it). There are a multitude of partial fixes available, starting with business process management (BPM) software, or Microsoft SharePoint, Google Drive, or Box-type workflow-based cloud content management solutions. These can be inexpensive but they lack defined applications and data management automation.
On the other hand, Master Data Management (MDM) software solutions can unite data and content but they lack the intelligence to execute processes and activities. And, as stated earlier, ERP and PLM systems alone don’t do it all.
Structured data (in rows and columns that can be easily ordered and processed with data mining tools) and unstructured data (raw/unorganized in emails, PDFs, images, video, audio) must be captured, processed, and conveyed accurately and seamlessly. But what’s missing in available solutions are the pre-built business objects, rules, and taxonomy that allow companies to process data, documents (managing the metadata), convert this captured data automatically, and/or manage business objects through easy, intelligent, forms-based systems.
Manufacturers need the ability to capture any required data from any source, document, or data stream. They need a solution that can overlap and/or fill in the gaps between PLM and ERP, and they need it to be flexible and cost-friendly to absorb change on an ongoing basis.
The Downside of Not Plugging ERP Data/Process/Operational Holes
Technical
information access and transparency across all internal departments and
critical external partners is the Holy Grail for companies in the process
manufacturing industries. Unlike services-centric businesses (which have
their own special needs), companies that procure materials elsewhere to embed
in their products face a set of extremely challenging quality, consistency,
compliance, and control issues attached to their products’ technical product
information management (PIM).
Here are just four of the many inherent issues that arise when data is
disconnected, not connected optimally, housed redundantly in silos, etc.:
- Inaccurate or out-of-date enterprise data. Most enterprise solutions assume information is both up to both date and consistent throughout—it’s not.
- Inability to easily amend PLM data and move into ERP. To get PLM data, add required data, and move it into ERP, many business have the object creation processes in current solutions that hit the master file boundaries, requiring manual entry, storing physical documents, or other stop-gap measures.
- External data sources are not well supported. Experts estimate that 70% of product-related data is externally generated and non-structured, yet most traditional enterprise applications are designed to primarily support internal, structured data. This requires manual re-entry or attachments to files (data that is not integrated into master files).
- Manual or redundant process resource bleeders. Companies lose time, money, and compromise auditability when they’re forced to use Excel trackers and reminder e-mails on things like regulatory/compliance requirements.
New AI-Infused Cloud PIM Solution Bridges PLM, ERP, CRM, and SRM
Clearly,
there is a good case to be made for a new category of manufacturing solutions
aimed at the problem of bridging the gap between process PLM, ERP, CRM, and SRM
solutions. What’s needed is a solution set that understands that
technical PIM has unique requirements, including the need to support continual
information inputs and iterations while also producing the insights that
process manufacturers need to survive and thrive.
Recently, it has come across Technology Evaluation Centers’ radar that a
process PLM-centric services provider, Oak Barrel Software, has
quietly expanded its company footprint to deliver an astute new, multi-tenant
cloud solution that addresses this market need. The company—without advanced
marketing fanfare in marketing—chose to instead introduce nine solutions aimed
at this technical PIM data gap problem to better quantify and qualify its
expanded business model and prove the value proposition of its new offerings.
Oak Barrel Software has added 20 customers only in Q1 2019 in the US,
Australia, and EMEA. The company will formally announce both a new name, and a
new market solutions category in a planned September 2019 PR/Industry Analyst
roadshow.
In a recent interview with Oak Barrel CEO Rory Granros, he advises that the new
solution is already delivering to its new customers the following capabilities:
- Immediate ROI via an incremental data input model (which can be turned on within 48 hours of licensing)
- Scalability at whatever pace the customer wishes to add data
- Improvements in quality/accuracy and efficacy of their newly introduced products
- Auditable compliance processes
- Automated data and document housekeeping processes to support operational and business process management
- Flexible, change-friendly capabilities
- Multiple publishing options: document management, in-memory databases, Walmart/Amazon marketplaces, the Global Data Synchronization Network (GDSN), ePIF (electronic product information form) portals, etc.
- Multi-level search capabilities across the value chain
- Continuous risk assessment
- Rate preference analysis
- Recertification prompts/alerts
- Portal-to-portal updates
“Oak Barrel has operated in the ERP/PLM space as a service provider for many years, and we know well where companies are struggling with skunk-works type solutions to a recurring set of technical product information issues,” explains Granros. “This technical product data impacts every area of process manufacturers’ operations – their need to manage, report, analyze, comply, and ensure quality and accurate communications. The problem is well substantiated as is the lack of a good solution; we are changing that. We have no equal competitors to what we are doing, so we’ll be creating our own market category. It’s the next generation of digitally transformative support in manufacturing.”
About Technology Evaluation Centers (TEC)
Technology Evaluation Centers (TEC) is a global consulting and advisory firm, helping organizations select the best enterprise software solution for their needs. TEC reduces the time, cost, and risk associated with enterprise software selection with its advanced decision-making process and support application, software selection experts, and extensive resources.
Over 3.5 million subscribers leverage TEC’s industry-leading research and detailed information on more than 1,000 leading software solutions across all major application areas. For more information, please visit www.technologyevaluation.com.