Plastics are widely used in the consumer goods industry, specifically the food and beverages segment. They are required for making containers that reach the consumers as well as the parts used in the food production process. However, one thing that you need to understand about the usage of plastics in this domain is that it has to be a food-grade variant. Essentially, this variant stays inert and non-reactive throughout its life cycle so that it does not react even as it comes in direct contact with food and beverages. It becomes imperative to look for a safe and effective technology to package and process the products. Thankfully, the process of plastic injection has you covered. Here are some ways it is making an impact on the food and beverage industry.
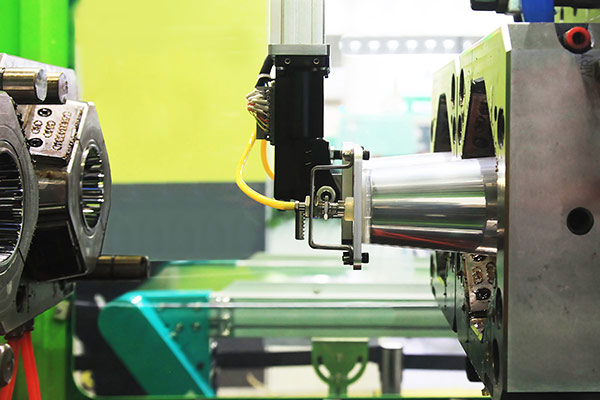
Diverse applications
The industry has diverse requirements in terms of packaging and processing the products and food-grade injection molding has you covered. It can be used for custom designing caps, containers, and straws. Further, it also works for creating temperature-resistant plastic containers for storage and serving food and beverage products. Other applications include processing equipment components and filtering components used in manufacturing processes for the industry.
High efficiency and fast production
Another reason why this molding technology is preferred is that it is highly efficient. The process is far quicker than any other method. At the same time, you can rely on it for a high production output rate which makes it cost-effective as well. The cost savings benefits are passed over to the consumer products and you end up getting higher revenue and profit margins for your business.
Complex parts designs
Considering the fact that the containers and equipment used in F&B have diverse and complex designs, you will need a method that has you covered on this front. Fortunately, plastic injection molding has the potential to handle highly complex parts and ensuring uniformity in them. You can trust it to create millions of virtually identical parts without any errors or compromise with quality. So you get an added benefit of consistency for your products.
Flexibility in material and color
Another factor that is important for the F&B industry is that you need plastics in different materials and colors for product packaging. With injection molding, you have the advantage of a wide variety of both. There is a large selection of resins from which you can choose, but you need to ensure that the molder sticks to the ones that comply with food safety regulations by the FDA, RoHS, REACH, and NSF.
Enhanced strength
With plastic injection molded parts, you can also rest assured about the strength factors. The process lets the designer ensure that the part is flexible or rigid according to the product specifications. You will have to decide it on the basis of factors such as how the consumer would be using the plastic part and what type of environment it will be exposed to through its lifetime.
Compared to other methods of plastic molding, injection molding emerges as the best one for food and beverage manufacturers. It is best to find the right partner for the process so that you can be used about the quality, sanitation, and integrity of your end product.