Industry 4.0 is the progressive step in a manufacturing company’s digital transformation maturity curve, focusing on combining information technology and operational technology to modernize the value chain in new ways.
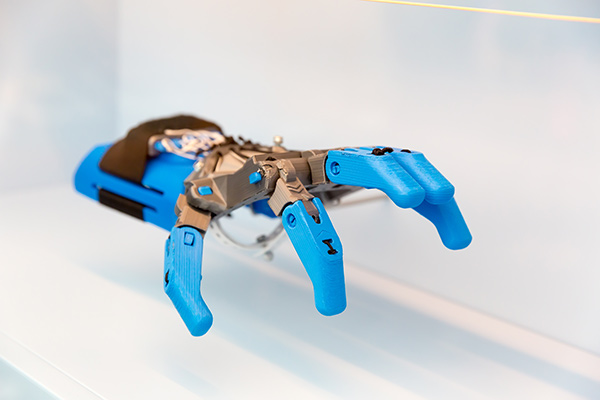
IIoT is one of the leading Industry 4.0 technologies that are fueling business growth for manufacturers. In simple terms, the Industrial Internet of Things (IIoT) is a framework that connects numerous industrial machines together with the help of sensors, devices, software, and the internet. Industrial machines that are connected together through the internet include robots, sensors, cranes, compressors, and more.
For our manufacturing customers, IIoT enables remote connectivity, monitoring, and predictive maintenance of their machines on the shop floor. Cloud, connected devices, sensors, artificial intelligence, big data, cyber-security, and additive manufacturing, are a few subcomponents of their IIoT strategy. With the help of interconnected systems, sensors, and devices, their manufacturing workforce can access the machines from their office, assess their performance, and view insights as well as log files remotely – anytime, anywhere.
Any variation or deviance from the set parameters can be identified by smart machines and communicated to those responsible for operating it. Also, intelligent sensors help automate the decision-making process on the shop floor.
When you install a new smart machine, it should be compatible with the existing setup and machines from the OEMs. Also, strong connectivity between the devices enables data sharing, establishes predictive maintenance, and minimizes security risks.
Industrial machinery often requires frequent maintenance. The good news is that with IoT-enabled ERP systems, manufacturers can preemptively know and predict when the operational failure of the industrial machine is imminent using sensors and cloud-based analytics.
Big players in manufacturing such as Boeing, Bosch, Airbus, etc. rely on IIoT for various reasons. Airbus has launched an initiative: Factory of the Future that focuses on wearable technology and integrated sensors which are designed for safety and reduced errors. Bosch launched a track and trace program that automates factory operations, tracks the workers, and guides assembly operations.
Cloud is an omnipotent component of IIoT-enabled ERP
The major objective of cloud ERP and IIoT is increasing organizational efficiency. We already know that IIoT is a framework of smart machines with embedded sensors and network connectivity. Cloud allows this framework to collect, send, and receive data without any manual intervention.
Cloud ERP and IIoT run parallel with each other. While IIoT generates a massive amount of data, cloud ERP creates a pathway for it to travel and reach its destination. Whether it is about tracking the data generated from machines or about knowing how many products have been procured and dispatched, cloud ERP lets you see everything from a single platform. In simple words, IIoT generates crucial data for the organization, and cloud ERP streamlines and protects it. A Gartner research says that IoT’s rapidly evolving technologies have ushered in innovative disruptions at a staggering pace, in five key areas:
Sensing — IoT endpoints
Communicating — IoT communications
Securing — IoT security
Understanding — IoT data and analytics
Acting — IoT artificial intelligence (AI)
Source: Gartner
Integrating ERP with IIoT leads to data availability in real-time. Integrating ERP software with IIoT transforms the supply chain drastically. How? When IIoT devices talks to your ERP applications, it promotes visibility at a detailed SKU level. For example, when you know that components you require for production are to be shipped internationally, ERP allows you to track the time of arrival as products are tagged and you get constant information of its whereabouts. ERP and IIoT applications work together to transform the way information is being received by us. It lets you monitor equipment and the production line 24/7.
Cloud is the gateway to modern manufacturing. It allows manufacturers to access information about the functioning of products after they have been shipped to the customers. Manufacturers can monitor the product’s behavior, its maintenance, wear and tear, and solve any problem that occurred in the product remotely.
How does Cloud ERP Enable IIoT in Manufacturing
Cloud ERP lays the foundation for collaboration, automation, and increased efficiency in a manufacturing environment. When you tie cloud ERP with smart industrial devices, it lets you see a holistic view of the shop floor and access data from anywhere and through any internet-enabled device.
IIoT primarily covers all industry sectors where industrial machines are used. It becomes easier for manufacturers to check the parameters, maintenance schedule, assembly process, and optimize different parts on the shop floor.
Cloud ERP brings every chunk of information in a single system. With integrated IIoT, manufacturers can more fully view accounting details, production completion status, inventory levels, customer input, defect (if any), shipment schedule, and minor details of everything happening on the shop floor.