The Internet of Things is rewriting the rules for all major industries, and manufacturing is no exception. The IoT connects machinery, infrastructure, products, and even people with a network of sensors, automation, and machine learning to create an environment in which business insights can be gleaned and applied virtually in real-time.
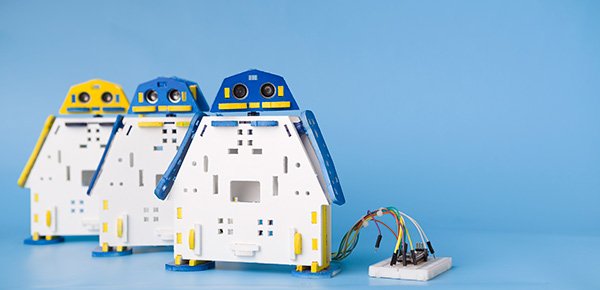
Line safety can be enhanced, and the complete spectrum of tasks and processes can be automated and optimized.
In fact, there are a number of compelling business benefits for leveraging the IoT in manufacturing – here are a few of the key ones:
Predictive maintenance.
Perhaps the most obvious benefit of the IoT is how it is disrupting traditional processes for performing equipment maintenance, moving businesses that embrace it from reactive maintenance to predictive and preventative.
The problem with the way maintenance is typically performed is that periodic maintenance can only be based on historical and statistical information, leading to unexpected work stoppages and a reactionary maintenance posture.
But by embedding sensors in equipment on the line, it’s possible to get detailed health and status data about individual equipment. That lets managers get out in front of maintenance issues and fix problems before failures would occur, disrupting operations.
Quality control.
It’s almost a cliché to say that customers are demanding ever-higher quality from the products they buy – and that’s true both for B2C and B2B manufacturing.
By integrating IoT sensors into the manufacturing workflow, though, it’s now possible to proactively manage manufacturing quality. Processes that require tight tolerances, for example, can be monitored by automated systems on a continuous basis.
Rather than discovering a problem during the QC stage after manufacturing – or worse, after the product has shipped and is in the customers’ hands – the IoT can identify when equipment falls out of tolerance, affecting manufacturing quality.
This can happen more or less in real-time, and regular analytics reporting can keep managers fully informed about quality control.
Safety and compliance.
Every shop and production floor has to contend with safety and compliance issues. Falling out of compliance can be expensive, have adverse regulatory consequences, and – especially when it comes to failing to meet OSHA requirements – can be dangerous for the people who need to work there.
One of the main reasons that safety and compliance is often so challenging for businesses is that the various reporting mechanisms are siloed and often not even digital. But the IoT allows all the data pools from the various compliance systems to be aggregated, shared, and synthesized in a wat that lets managers truly manage the floor in a holistic way.
Real-time monitoring provided by sensors can feed compliance reporting. And emerging technologies, like machine learning AI systems that monitor camera systems, can ensure workers are wearing personal protective equipment and using equipment safely and according to requirements.
Energy efficiency.
Energy costs are a substantial expense in any manufacturing operation, but most businesses have only a rudimentary understanding of exactly where all the energy dollars actually go.
Even detailed billing data provided by the power company is often insufficient to make practical strategy decisions. That’s where the IoT can help.
With the right instrumentation, all the equipment on the manufacturing floor can report its energy consumption, which can be turned into analytics for managers.
That means it’s possible to get insights into how to operate more efficiently and where there’s waste in the workflow.
The IoT can reveal how to change production schedules to more efficiently use energy-hungry equipment, and even when similar machines have different energy consumption profiles – which in turn can suggest the need for maintenance or changing processes.
The bottom line is that the IoT can reduce downtime due to failures, dramatically improve regulatory compliance and safety concerns, save money energy bills, and help the end product be produced at a higher quality.
These benefits are just scratching the surface, though, because the Internet of Things can also play a role in improving inventory and warehouse management, procurement, transportation, and more. And, with 5G coming over the horizon, things get even more interesting. Manufacturing faces an amazing future.