Did you know that today’s ERP systems evolve from the MRP systems of the past? If you are interested in the differences, applications and functionality of MRP and ERP, this article is for you!
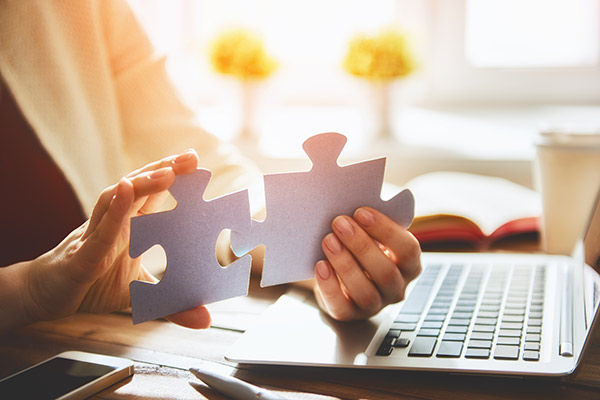
Understanding the difference between ERP and manufacturing resource planning (MRP) is important to getting the most out of these systems. Today’s ERP systems evolved from yesterday’s manufacturing resource planning (MRPII) systems that were based on material requirements planning, the original MRP that started it all. Remnants of MRP still form the backbone of most ERP systems. Even advanced planning and scheduling (APS) and distribution requirements planning (DRP) systems can trace their roots back to the original MRP.
What is MRP?
The key to understanding the difference between ERP and MRP is to trace the evolution of this software category from its inception more than half a century ago. Early mainframe computers were first used only for simple storage, retrieval, sorting and straightforward calculations. The breakthrough for manufacturing came with the development of a way to recognize relationships between parts, assemblies and products — the bill of materials that is the basis of material requirements planning (MRP). MRP is a calculation of what parts and materials are needed to make an assembly or product, as well as when those components are needed based on the due date for the final product.
MRP requires inventory balances and availability, production and purchasing lead times and current order status, as well as forecasts and customer orders that drive the master production schedule. As a result, inventory management, production control, customer order management and purchasing applications were developed and integrated into a comprehensive software suite that also included accounting applications, resource planning and production scheduling and was eventually named manufacturing resource planning or MRPII.
MRP vs. ERP
MRPII continued to grow year after year as the integrated applications matured and expanded and new ones were added. These improvements — along with adaptations to take advantage of computing advances like relational databases, natural language query and optimization technologies — were not reflected in the market’s perception of MRPII, which was seen as old and outdated. Thus a new acronym was invented: ERP. Today, the term MRPII has virtually disappeared. However, there is some incorrect use of the term MRP to refer to inexpensive, less capable manufacturing software suites marketed to small companies.
ERP is the integrated software suite that manages the majority of company information. ERP develops and monitors the execution of plans that are created in the MRP application or, optionally, an advanced planning application that can replace or supplement MRP. ERP is the name for the integrated suite and MRP is the planning application contained therein.
Features of ERP systems
ERP systems are generally developed as modular applications that address specific areas of the business. In addition to the core modules that support basic records — items, bills of materials, resources and routings — and modules for inventory management, manufacturing operations, purchasing, customer orders, planning and finance, most systems have additional modules that make the system more complete. These include human resources as well as support for business functions that not every company needs, such as field service management, deeper quality management functionality, advanced planning and finite scheduling. The ability to mix and match these optional modules provides a way to tailor the system to fit specific industries like food and beverage, industrial equipment, electronics, consumer goods or process manufacturers.
Types of ERP software
MRPII and ERP were developed to support the information management needs of manufacturers and distributors. More recently, the term ERP has become the general name for any integrated business management application suite. You can now find ERP systems for retail, services businesses, wholesale distribution, utilities, hospitals and just about any other kind of business you can think of.
These ERPs usually contain the same or similar functionality for the basic processes that all businesses share, such as customer order management, billing and collection, inventory management, financial accounting, payroll and human resources and, in addition, specific needs of their business, like dispatching personnel and vehicles, scheduling appointments or tracking service use.