In this exclusive interview, Carter Lloyds, Chief Product Officer at QAD, shares insights into the company’s recent acquisition of Phenix Software, a strategic addition to elevate QAD’s Advanced Scheduling capabilities. Selected for its robust industry-specific features and exceptional user experience, Phenix Software now powers QAD Advanced Scheduling. Carter discusses how this solution empowers manufacturers to optimize production sequencing, reduce changeovers, and enhance resilience against workforce challenges—all essential for today’s adaptive enterprise. Discover how QAD’s advanced scheduling solution integrates seamlessly with its ERP suite to bring real-time adaptability and efficiency to the manufacturing floor.
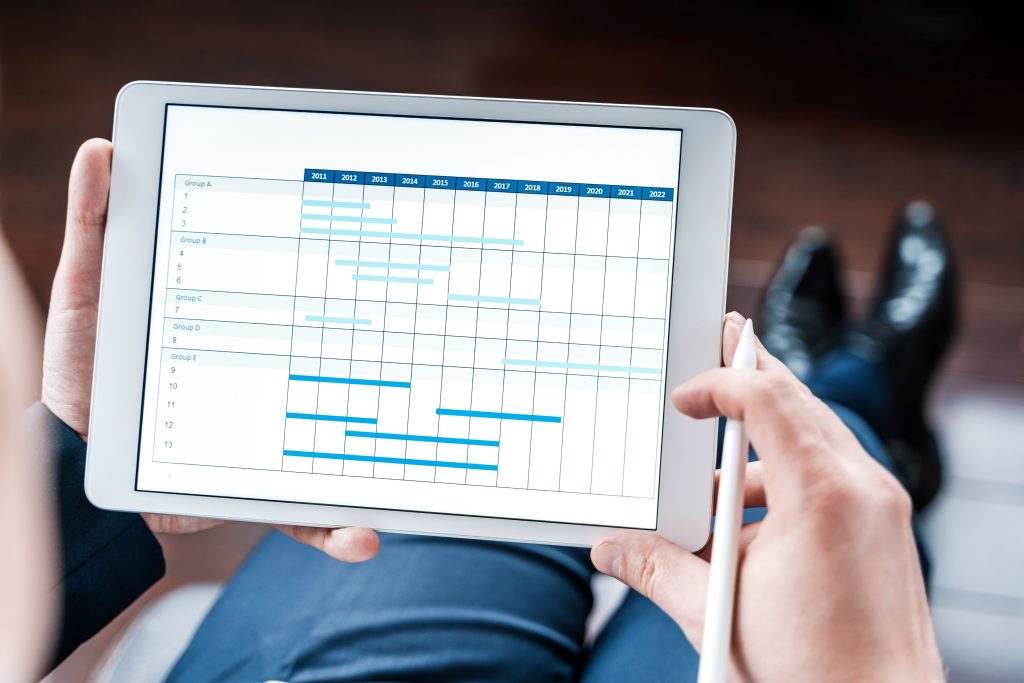
- What drove QAD to acquire Phenix Software, and how does this acquisition align with QAD’s long-term strategy?
QAD began the search for an advanced production scheduler in early 2023; the initial intent being to bridge the gap between planning and scheduling by complementing our industry-leading Digital Supply Chain Planning (DSCP) solution. At the same time, we were looking to uplift our current Master Scheduling Workbench / Production Scheduling Workbench (MSW/PSW) offering that is bundled with our ERP with enhanced functionality and a fully web-based user interface.
After evaluating 69 solutions, we shortlisted 17 and selected Phenix based on its vertical industry support, process and discrete functionality, strong multi-level, multi-line capabilities and rich interactive user experience including drag-and-drop Gantt charts.
Phenix will support QAD’s vision for the Adaptive Enterprise given scheduling improvements directly impact efficiency. This can increase the effective capacity of your plant and mitigate the impact of workforce shortages. Manufacturers will be able to increase production beyond what was previously possible without capital investment while improving resilience against employee attrition. Combined with QAD ERP, QAD Connected Workforce and QAD DSCP, QAD and Phenix customers can optimize the entire flow from planning through scheduling to execution. It has been said that you can not schedule yourself out of a bad plan; a holistic view across planning, scheduling, and execution helps identify and solve root-cause problems that would otherwise lead to suboptimal performance.
- Could you explain the primary benefits QAD Advanced Scheduling brings to manufacturers?
Phenix specializes in Production Scheduling Software designed to help manufacturers optimize their operations. Their solutions assist businesses in scheduling and managing production processes more efficiently. By leveraging advanced algorithms and real-time data, Phenix’s software aims to improve productivity, reduce operational costs and enhance overall efficiency.
Key Features:
- Advanced Production Scheduling (APS): Optimizes production schedules by considering resource constraints, deadlines and demand forecasts.
- Real-Time Data Integration: Connects with existing ERP and MES systems to provide up-to-date information on production status.
- Resource Management: Efficiently allocates machinery, labor and materials to maximize output and minimize waste.
- What-If Analysis: Enables simulation of different production scenarios to support informed decision-making.
- Analytics and Reporting: Offers insights into key performance indicators through customizable dashboards and reports.
Benefits:
- Increased Efficiency: Streamlines production workflows to reduce downtime and eliminate bottlenecks.
- Cost Reduction: Enhances resource utilization, leading to lower operational expenses.
- Improved Delivery Times: Boosts the ability to meet customer deadlines through better scheduling and forecasting.
- Enhanced Visibility: Provides comprehensive oversight of production processes for proactive management.
- How does advanced scheduling optimize production sequences and help minimize changeovers?
Advanced Scheduling uses product attributes such as pack configuration, brand, label type, and allergens to determine the individual changeover activity between any two production activities. For example, cleaning a filler from a product containing nuts to a product with no nuts takes ‘x’ hours. The opposite sequence may be ‘y’ hours. There is no limit to the number of attributes. Multiple changeover activities (filler, labeller, palletizer) can be configured to occur in serial or parallel depending upon the tools and labor required. When generating a schedule the solution can use product wheels to ensure non-productive time (cleaning, setups, changeovers) is minimized by allocating production of alike attributes (or changeover friendly attributes) in an optimal sequence. Allergenic products are batched together and occur after regular products. Paint production will be sequenced from light to dark color. Filler equipment will batch together similar pack configurations. The approach minimizes the effort to maintain changeover data as values are managed by attributes, not SKUs.
- In what ways does QAD Advanced Scheduling support manufacturers’ goals for agility and resilience?
In addition to improving labor efficiency, QAD Advanced Scheduling enhances resilience against both unexpected machine downtime and workforce challenges. By optimizing production sequences, the system allows for quick reallocation of tasks, whether it’s adjusting to a machine breakdown or a sudden worker shortage. This built-in flexibility ensures that even when disruptions occur—whether from equipment failure or absent employees—the production line continues running smoothly with minimal delays.
For the workforce, QAD Advanced Scheduling makes labor more efficient by ensuring that workers are allocated optimally, minimizing idle time and maximizing productivity. This efficiency creates more room in the schedule to absorb the impact of high turnover or absenteeism. If workers are unavailable, the system can quickly adjust and redistribute tasks without significant loss of output. This reduces the pressure caused by worker shortages, making the operation more resilient. With more room in the schedule, shifts can be extended or added if needed.
Moreover, by increasing the effective capacity of the plant—through more efficient use of labor and equipment—the company becomes more agile. This enhanced capacity means the business can absorb unexpected surges in demand that it otherwise would not have been able to fulfill. With more room to maneuver, manufacturers can quickly scale up production to meet these demands and bounce back from unexpected disruptions.
- The most important customer-facing items we have in plan for the next year.
Closed Loop Scheduling
QAD will use its unique position as a provider of best-in-class Production Scheduling and Factory Workforce Collaboration solutions to close the loop between planning and execution. This involves a tight bidirectional integration between QAD Advanced Scheduling and QAD RedZone. Production schedules can be published in real time disseminating crucial schedule changes to the factory floor. In turn, actual factory floor activities such as unforeseen downtime or delayed starts can be published back to Advanced Scheduling allowing the schedule to be automatically adjusted to absorb the impact of the event. Often there is a lag between a current real-time event (e.g. delayed start, overrun) and the consequent constraint violation. The early detection provides more options for resolution and minimizes the impact on the production schedule. This greatly improves the agility of a manufacturer to respond in an optimal manner to unforeseen events. The closed loop is enhanced even further when connected to QAD ERP so changes in material advanced shipping notices can be incorporated into the material constraints of the schedule in real-time. This provides our customers with a synchronized and optimized operational plan that is highly responsive to near-term disruptions.
Operations Centric Scheduling
Most scheduling solutions operate at the Production Order level. Production Orders generated by MPS/MRP processes are sequenced in a capacity-constrained manner across the production timeline sensitive to material, labor, and tooling availability. In the next year QAD Advanced Scheduling will allow production orders to be expanded into a lower level of operations prior to being scheduled. The Operations may be non-production related (sterilize equipment, calibrate a scale, take a QA sample) or production-related (paint, weld, sort, quality check). Once the Production Orders are translated into sequenced operations, then alike operations are grouped, allocated a work center, and scheduled. This finer granularity of operation scheduling is critical to resolving work center constraints and improving throughput efficiency. This is table stakes in high volume discrete repetitive environments such as Automotive and A&D.
Holistic Optimization
QAD Advanced Scheduling uses the concept of Product Wheels to optimize production sequences across the scheduling horizon. Product Wheels have proven to generate feasible and planner intuitive schedules. QAD Advanced Scheduling will continue to support the product wheel approach. In addition, to support highly complex production environments with dynamically floating, multi-stage bottlenecks that change depending upon the product mix, QAD will also provide a holistic optimization engine that can generate a finite capacity schedule based upon a set of objective functions. Objective functions will include: minimizing non-production time (for highly constrained factories); minimizing production span (duration from consumption of raw material to generation of finished product across all production stages) for factories with shelf-sensitive intermediate product or in-factory inventory staging constraints; balanced workload (for factories with high labor costs), in addition to a series of sub-vertical niche objectives used in specific industries.
- How does the new solution integrate with QAD’s existing suite of manufacturing and ERP tools?
QAD Advanced Scheduling compliments the existing QAD manufacturing solutions including the manufacturing system of record (QAD ERP), decision support (QAD DSCP), and factory floor execution (QAD Redzone Connected Workforce). QAD Advanced Scheduling will plug into the QAD Integration Framework publishing schedules and subscribing to orders and inventory positions that are published by QAD ERP. Likewise, QAD DSCP will publish capacity-constrained weekly manufacturing requirements which will be shared with Advanced Scheduling to generate sequenced time-phased production activities. An important differentiator is the link between Advanced Scheduling and the workforce collaboration capabilities of QAD Redzone. This will allow schedule changes to be instantly published to the floor and actual production results to feed back into the schedule. This improves the visibility and agility of the factory.
- What unique capabilities does Phenix Software offer that other scheduling solutions do not?
QAD Advanced Scheduling has very clear differentiation in “closed loop” scheduling. In the past, manufacturers invested heavily in complex optimization tools and data cleansing processes to mathematically build the purest optimal schedule the first time. In some cases this was the full extent of the scheduling processes. In today’s hyper-connected manufacturing landscape, the “perfect” schedule becomes obsolete in a matter of minutes. As soon as a job starts late, a production batch is out of spec, something breaks on the line, or materials arrive late; the schedule is being automatically updated with real-time data feeds, some of which will trigger potential constraint violations. The close-loop scheduling capabilities of QAD Advanced Scheduling then becomes a firefighting tool for the scheduler. This greatly enhances the value proposition of an Advanced Scheduling tool. Not only is OEE and resource utilization improved, there is earlier detection and resolution of potential disruptions. The reduced impact of potential disruptions reduces chaos and improves schedule performance. The cohabitation of QAD Advanced Scheduling and QAD Redzone offers a unique capability to synchronize scheduling and execution.
- How does the solution help manufacturers balance cost and service goals while managing inventory and capacity?
QAD Advanced Scheduling optimizes production schedules by creating the best sequence of tasks, reducing unnecessary changeovers and minimizing downtime. This directly reduces time spent on unproductive activities, such as machine setup or waiting for materials. By minimizing these delays, manufacturers can increase the effective capacity of their plants without needing to add more shifts or machinery, which reduces labor and operational costs.
The streamlined scheduling also reduces the need for excessive safety stock or buffer inventory, as production is more closely aligned with demand. With fewer disruptions, inventory levels can be kept lower, which reduces holding costs such as warehousing and spoilage, improving overall efficiency.
This optimized approach also enhances service levels by ensuring that the right products are produced and delivered on time. By efficiently meeting customer demand without overproducing, manufacturers can lower costs related to expedited shipping or penalties for late deliveries, while increasing customer satisfaction with better on-time performance. The result is a dual benefit of lower operational costs and higher service quality.
- What role will Phenix Software play in supporting and implementing QAD Advanced Scheduling moving forward?
Phenix started as a collaboration of highly experienced planning and scheduling practitioners at Zinata Inc., who identified that customers were experiencing major performance loss due to suboptimal changeovers and inventory levels, with no suitable tool to sustain the gains made with existing scheduling solutions. With a shared commitment to providing the best scheduling solution possible, Zinata Inc. has become a QAD Distributor to sell, support, and implement the product as a valued partner. Zinata’s vast experience in manufacturing and scheduling will provide continued expert support, benefiting our current and future customers.
- How does QAD plan to expand the reach of QAD Advanced Scheduling in the global market?
QAD has the infrastructure to bring Advanced Scheduling to new regions, industries, and customers, ensuring a seamless deployment across diverse markets. Our broad network of partners allows QAD to penetrate markets where local expertise is crucial, further enhancing the global reach of the solution.
QAD Advanced Scheduling is a natural fit for our existing QAD ERP, QAD Digital Supply Chain Planning (DSCP), and QAD Redzone Connected Worker customers. These customers already rely on QAD solutions to optimize other parts of their operations, and integrating Advanced Scheduling will enable them to further streamline production, improve capacity management, and respond more effectively to market demands. Our large global customer base provides an immediate opportunity for cross-selling and extending the value of QAD’s broader solution suite.
This strategy positions QAD to not only serve new customers but also to enhance value for existing ones, driving adoption of Advanced Scheduling across multiple industries and geographies.