SAP today announced new use cases to help optimize spare part replenishment, procurement and distribution within supply chains of service and maintenance-intensive companies.
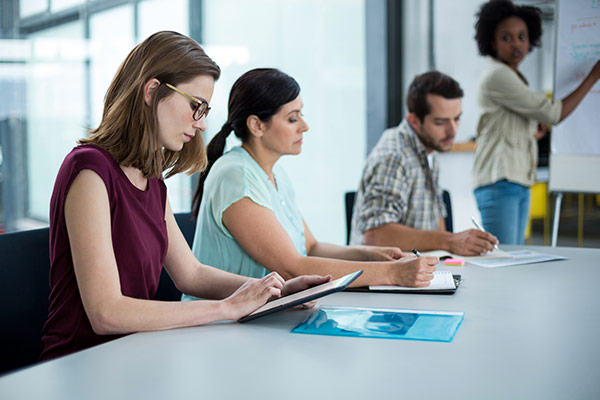
These are the result of SAP’s intelligent supply chain for assets customer initiative, which brought together SAP and more than 45 customers to co-innovate in this mission-critical area. The announcement was made at the North American Supply Chain Executive Summit in Chicago.
“Every business leader I meet is looking for new ways to procure, manage and maintain aging assets to ultimately deliver on the desires of their customers,” said Franz Hero, SAP senior vice president, Digital Supply Chain Development. “With this initiative, we went straight to the source, working directly with our valued customers to explore new techniques and come up with real-world answers. Together, we’ve found a fresh approach to supply-chain planning and asset management to benefit everyone.”
The customer collaboration yielded two main scenarios that existing and new customers can take advantage of today to help them plan spare parts, as well as road maps to enhance these scenarios as part of SAP’s strategy for digital supply chain.
- The SAP Integrated Business Planning solution can be configured with standard templates, integrating maintenance repair and overhaul (MRO) processes with demand planning, maintenance planning and inventory optimization. As a result, customers avoid unexpected maintenance delays due to lack of spare parts. This is an ideal approach for asset-intensive industries such as oil and gas, utilities and chemicals to increase asset availability and reliability.
- The service parts planning solution from SAP helps organizations in industries such as automotive and aerospace and defense with forecasting, inventory planning, procurement and distribution of large volumes of service parts to their customers in order to maintain targeted service levels. The application will be available on SAP S/4HANA, making it ideal for companies that distribute large volumes of aftermarket service parts to numerous stocking locations.
“Working with SAP, we were able to gain a better understanding of how our parts planning approach can be developed further,” said Christian Faltus, Swiss Federal Railways SBB head of Procurement and Spare Parts Dispatching. “Maintenance planning and parts planning have been two separate processes so far. With the initiative, we hope to bring both worlds together and ensure that supply chain profits from maintenance optimizations such as condition and predictive maintenance. We’re looking forward to innovations from SAP to reduce asset downtime from missing parts.”