The manufacturing industry has seen significant advancements over the years, and cutting tools have evolved just as rapidly. From the early days of manual cutting tools to the high-precision machines we see today, cutting-edge technologies have shaped the capabilities of industries worldwide.
Traditional cutting methods, such as mechanical blades and hand tools, have given way to sophisticated, automated solutions that can meet the demands of modern manufacturing. These advanced tools improve accuracy, reduce waste, and speed up production processes, which in turn lowers costs.
In this article, we will learn in detail about the different technologies available and how they can help industries!
Read on!
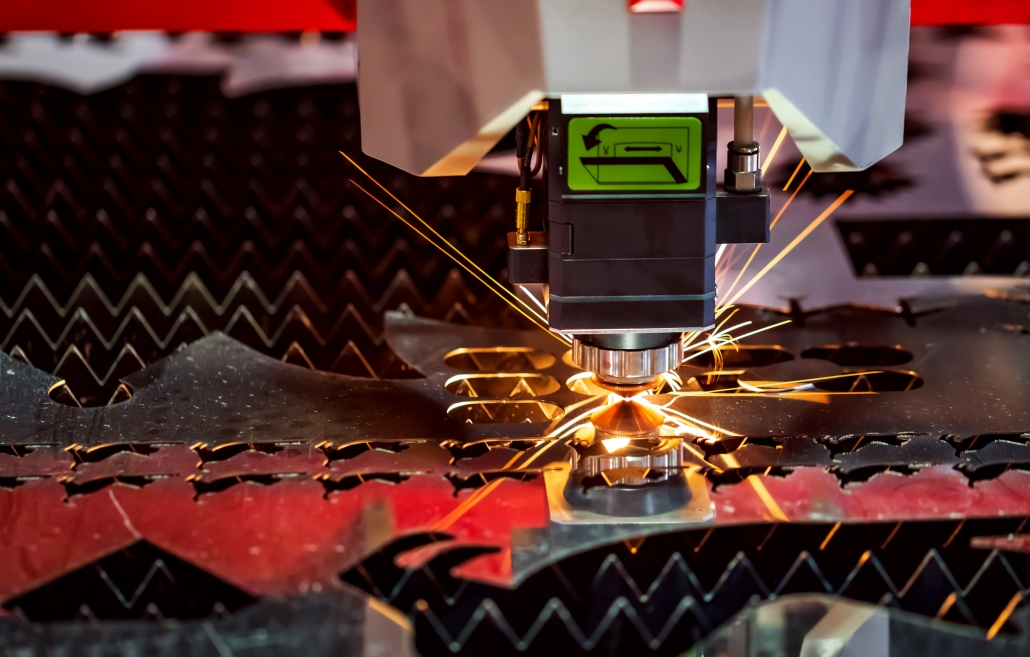
Types of Next-Generation Cutting Tools
Laser Cutting Tools
Laser-cutting technology has become one of the most popular tools in modern manufacturing due to its unmatched precision and speed. A laser beam, guided by computer control, is used to cut materials with extreme accuracy. It can handle intricate shapes and patterns that traditional tools struggle to achieve, making it ideal for aerospace, automotive, and electronics industries, where precision is paramount.
One of the major benefits of laser cutting is the minimal waste it produces. Because the laser beam is so fine, it removes only a tiny portion of the material, which means less waste compared to other cutting methods. Additionally, it can work with various materials, from metals to plastics, providing flexibility across industries.
Plasma Cutting
Plasma cutting is another widely used technology for cutting thick and conductive metals. The process involves generating an ionized gas (plasma) to create an electric arc, which easily cuts through the material. Plasma cutting is known for cutting through thicker metals quickly and efficiently. It is commonly used in construction, shipbuilding, and heavy machinery manufacturing industries.
People often face the challenge of deciding between laser cutting and plasma cutting. While both are efficient, their applications can differ based on material thickness, cost, and precision requirements. For clarification, you can read articles on laser cutting vs plasma cutting to explore the differences between choosing the right method for your needs. Understanding the specifics will help industries make an informed decision based on their project’s requirements.
Waterjet Cutting
Waterjet cutting is a versatile technology with a unique benefit: it uses no heat. Instead, it relies on a high-pressure jet of water, often combined with abrasive particles, to cut through materials. This makes it ideal for heat-sensitive materials, such as rubber, plastics, and some metals.
It is widely used in industries like aerospace and automotive, where the integrity of the material must remain unaffected by heat. It can also handle a variety of materials and thicknesses, adding to its flexibility. It’s also an environmentally friendly option, as it doesn’t produce harmful fumes or hazardous waste during the process.
CNC Cutting Machines
CNC (Computer Numerical Control) cutting machines have revolutionized manufacturing by automating cutting operations. Using programmed software, CNC machines can make precise cuts with minimal human intervention. They are used across various industries, from automotive to electronics and furniture manufacturing.
The primary advantage of CNC machines is their ability to produce high-precision parts with little error consistently. Automation reduces the need for manual labor, decreasing the risk of human error and improving overall productivity.
Benefits of Next-Generation Cutting Tools
Improved Precision
One of the biggest advantages of next-generation cutting tools is their ability to provide ultra-precise cuts. Whether using lasers, plasma, or CNC machines, these technologies ensure that each cut is accurate to the millimeter. This level of precision improves the overall quality of the product and reduces the chances of defects.
Increased Speed and Efficiency
Another significant benefit of modern cutting tools is faster cutting times. Automated processes allow for continuous operation, meaning production can move quickly without sacrificing quality. This increased speed translates to higher productivity and shorter project timelines, making it easier for businesses to meet demand and reduce downtime.
Reduction in Material Waste
Modern cutting technologies are designed to optimize material usage. By producing cleaner cuts with minimal waste, these tools help manufacturers reduce costs associated with wasted materials. This is particularly important for expensive materials, where waste can be costly.
Flexibility Across Materials
Next-generation cutting tools are versatile and capable of working with various materials. Tools like laser cutters, waterjets, and CNC machines can handle different textures, densities, and thicknesses, from metals and plastics to composites and rubber. This flexibility allows manufacturers to take on diverse projects without needing multiple tools.
Enhanced Safety Features
Safety is a top priority in manufacturing, and next-gen cutting tools have advanced safety features. Automated processes, remote operation capabilities, and reduced manual handling help minimize the risk of injury. Modern cutting tools are also designed to create cleaner work environments by reducing fumes, heat, and debris.
Closing Lines
Next-generation cutting tools are transforming industries by offering unparalleled precision, speed, and efficiency. Embracing these advanced tools is crucial for businesses to stay competitive in today’s fast-paced market. Manufacturers can make informed decisions that lead to higher productivity and product quality by carefully considering factors such as material type and consulting with experts.