Quality control testing is a critical aspect of industrial safety, ensuring that processes, products, and equipment meet established standards and regulations. It plays a vital role in preventing accidents, protecting workers, and maintaining the integrity of operations. Implementing rigorous quality control measures helps industries mitigate risks, enhance efficiency, and maintain compliance with safety regulations.
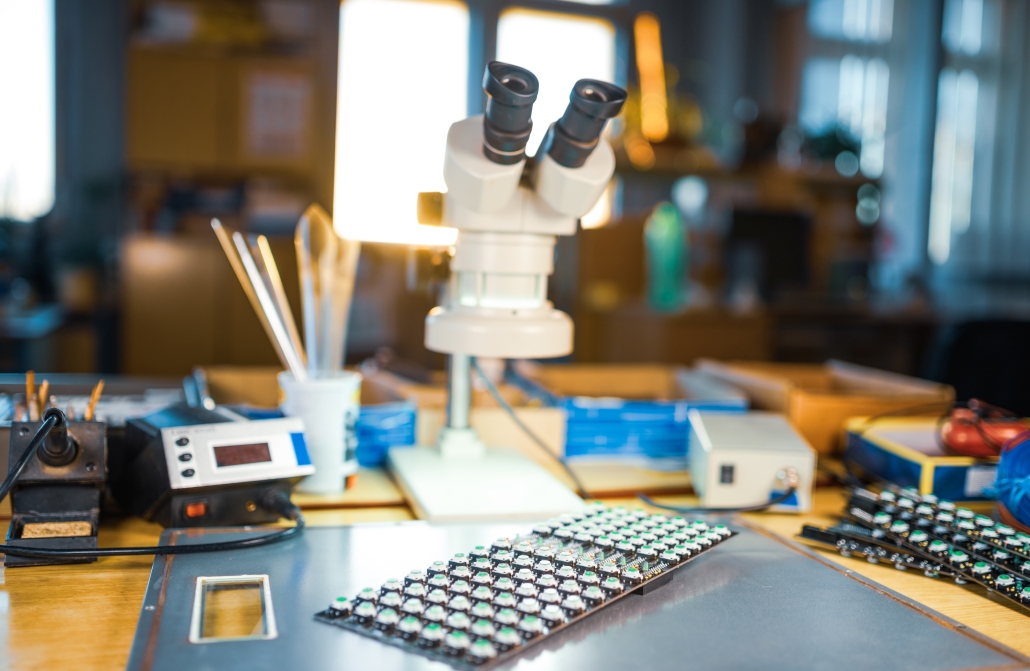
Importance of Quality Control Testing
Quality control testing is essential for several reasons. It helps identify defects and inconsistencies in products and processes before they reach the market or become operational. By catching these issues early, industries can prevent costly recalls, equipment failures, and accidents. Moreover, quality control testing ensures compliance with national and international safety standards, protecting companies from legal liabilities and reputational damage.
Types of Quality Control Testing
There are various types of quality control testing used in industrial safety, each serving a specific purpose:
- Material Testing: This involves testing raw materials to ensure they meet the required specifications. Methods such as tensile testing, hardness testing, and chemical analysis help determine the material’s suitability for use in production.
- Non-Destructive Testing (NDT): NDT methods, including ultrasonic testing, radiographic testing, and magnetic particle testing, are used to inspect materials and components without causing damage. These tests help detect internal flaws, cracks, and other defects that could compromise safety.
- Destructive Testing: Unlike NDT, destructive testing involves testing materials or products to the point of failure. This helps determine their strength, durability, and performance under extreme conditions. Common methods include impact testing, fatigue testing, and fracture toughness testing.
- Functional Testing: This type of testing ensures that equipment and systems operate correctly and safely. It includes tests such as pressure testing, leakage testing, and performance testing to verify that all components function as intended under normal and abnormal conditions.
- Environmental Testing: Environmental testing assesses how products and materials perform under various environmental conditions, such as extreme temperatures, humidity, and corrosive environments. This is crucial for industries operating in harsh environments to ensure their products can withstand the conditions.
Implementing Quality Control Testing
Effective implementation of quality control testing involves several key steps:
- Establishing Standards and Procedures: Developing comprehensive testing standards and procedures based on industry regulations, best practices, and specific operational requirements, such as mandatory signs. These should be well-documented and easily accessible to all relevant personnel.
- Training and Certification: Ensuring that all personnel involved in quality control testing are properly trained and certified. This includes understanding the testing methods, equipment operation, and safety protocols. Continuous training and certification updates are essential to keep up with technological advancements and regulatory changes.
- Utilising Advanced Technology: Incorporating advanced testing technologies and equipment to enhance accuracy, efficiency, and reliability. Automated testing systems, for instance, can reduce human error and provide more consistent results.
- Regular Testing and Maintenance: Conducting regular quality control tests and maintenance checks on equipment and processes. This helps identify problems quickly and ensures ongoing compliance with safety standards. Establishing a routine testing schedule is critical for consistent safety assurance.
- Documentation and Reporting: Maintaining detailed records of all quality control tests, including test results, methods used, and any corrective actions taken. This documentation is essential for audits, compliance verification, and continuous improvement efforts.
- Continuous Improvement: Quality control testing should be a continuous process aimed at constant improvement. Regularly reviewing and analyzing test results can help identify trends, areas needing improvement, and opportunities for innovation. Encouraging feedback from personnel is essential to refine testing procedures and enhance overall safety.
Conclusion
Quality control testing is vital for industrial safety, offering a structured method to identify and mitigate risks. By establishing rigorous testing protocols, industries can ensure process and product integrity, safeguard their workforce, and adhere to safety regulations. Ongoing improvement and adaptation to new technologies and standards are essential for maintaining high safety levels and operational excellence. Through diligent quality control testing, industries can achieve safer, more efficient, and reliable operations.